EXECUTIVE SUMMARY
The important role of fasteners in ensuring safe and reliable solar racking and tracking structures is critical but often underappreciated. There are significant differences in strength and performance between the two main types of fasteners—threaded and lockbolt.
This paper compares threaded and lockbolt fasteners and finds that lockbolts offer distinct advantages over traditional threaded fasteners for connecting permanent PV racking system joints.
SITUATIONAL ANALYSIS
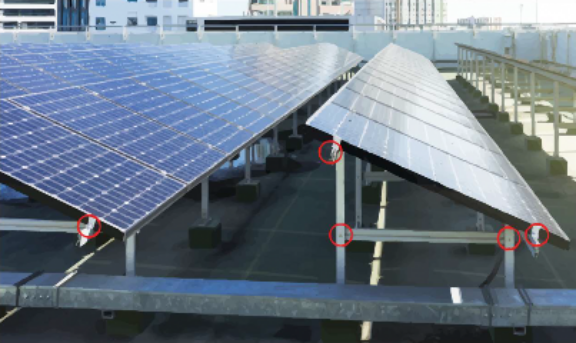
Some of the most overlooked components within a photovoltaic (PV) racking and tracking system are the fasteners. Although relatively simple and inexpensive components, fasteners play a critical role in the structural integrity of PV systems. Each fastener connects two or more components to create a securely fastened joint that transmits both static loads (live, dead and snow) and dynamic loads (wind). In some systems, the joint also serves as a low-resistance electrical conduction path for grounding purposes. A typical PV system contains thousands of fasteners, underscoring the critical role they play in the structural reliability and safety of the system, as shown in Image 1. A wide variety of fastener designs and materials are used in PV racking system joints and they can generally be categorized as either traditional threaded fasteners (nuts and bolts) or lockbolts as shown in Image 4.
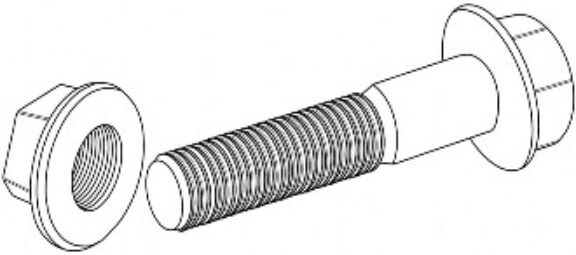
Nuts and bolts have been around for hundreds of years, and although there have been improvements in the thread form and in standardization, the basic design has remained the same. The nut is connected to the bolt through threads in both components (see Image 2). Assembly is accomplished by simply rotating the nut relative to the bolt and applying a torque which results in preload (clamp load) in the joint. Threaded fasteners can be tightened manually using relatively inexpensive torque wrenches, or if assembly speed is critical, they can be tightened using portable electric torque tools. Compared to other forms of joining, the threaded connection allows the fasteners to be assembled and disassembled easily. While traditional threaded fasteners are relatively low cost, they can be a source of significant problems in PV racking systems.[1]
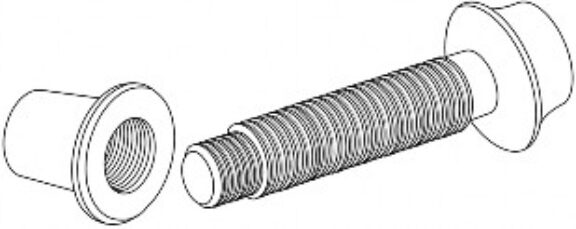
The lockbolt consists of a high-strength bolt and matching collar made from softer material (see Image 3). Lockbolts have been widely used in automotive, aviation, rail, agriculture, mining, military and other applications that experience severe dynamic loads and are now commonly used in PV racking and tracker systems. Similar to a threaded fastener, the lockbolt is initially assembled by rotating the collar relative to the bolt, but instead of applying torque, a special powered installation tool is used to stretch the bolt and crimp the collar over the threads, which results in a predetermined preload and clamp load.[2,4] Lockbolts can often be assembled in less than 5 seconds. The expense of the special installation tools and equipment required for assembly could be uneconomical for small quantities but that is generally not an issue with PV racking systems given the large number of fasteners. Most lockbolt joints are considered both permanent and tamper-proof. Like threaded fasteners, lockbolts are available in a variety of carbon and alloy steels, aluminum and stainless steel materials, making them ideally suited to joints exposed to the environment like PV racking systems.
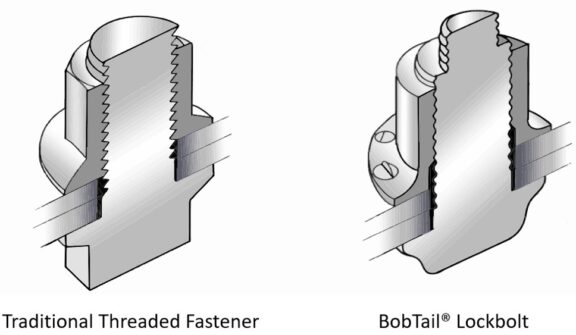
The UL 2703 standard for PV mounting systems requires racking joints to be slip-resistant and to stay closed under the anticipated loads. In most PV racking joints, the loads are transmitted through the joint interface through the preload and resulting clamp load that develop in the fastener during the assembly process. If the residual preload in the joint can’t handle the loads experienced in service, the joint components will separate or slip, or both, and if this joint movement happens repeatedly, the fastener connecting the joint will likely fail due to fatigue. Developing and maintaining the fastener preload and clamp load throughout the life of the PV installation is critical to the reliability of the PV racking joint in service. [1,2,3,5,6,7]
Regardless of whether the fastener is a threaded fastener or a lockbolt, its primary purpose is to develop and maintain clamp load in the racking system joint throughout the life of the installation. Based on the work completed by NEXTracker and others, it has been shown that lockbolts offer distinct advantages over threaded fasteners for joining permanent PV racking system joints. [8]
ISSUE: PRELOAD SCATTER
One inherent problem of torque-tightening threaded fasteners is the significant scatter or range of values of the preload achieved through the assembly process. The preload scatter results from inaccuracies in the tightening torque, in the friction coefficients, in the sliding interfaces, in the fastener, and the skill of the assembler. These inaccuracies can result in variations in the preload of a torque-tightened threaded fastener, ranging from ±25% on the low end to as much as ±60% on the high end as shown in Diagram 5. [3]
Accuracy of Tightening Torque
A typical PV racking system includes a tremendous number of fasteners, so assembling and tightening fasteners is a significant undertaking. Some companies tighten the fasteners manually using a clicker-style torque wrench, while others use cordless electric nut-runners or impact wrenches. Calibrated, clicker-style torque wrenches and precision cordless nut runners can deliver a torque accuracy of approximately ±10% when used by a skilled and trained assembler. In contrast, impact wrenches deliver torque accuracy as low as ±40% or worse, regardless of the assembler’s skill [3]. Because of the inaccuracy of the tightening-torque technique and tools used during assembly, many PV racking joints enter service with lower preload than expected, unless a consistent quality control program is in place to audit and correct the assembled torque.
Friction Coefficients
The final preload achieved in a torque-tightened fastener also depends on the friction coefficients in the sliding interfaces such as the threads, the nut, or the bolt-bearing surfaces, whichever is rotating. Stainless-steel fasteners are frequently used in PV racking systems because of their corrosion resistance. Unfortunately, the friction coefficients in stainless steel are high, especially if lubrication is not applied to the threads and sliding-bearing surfaces. To make matters worse, stainless-steel threaded fasteners tend to gall during assembly especially if prevailing lock nuts are used. A thin layer of chromium oxide protects stainless fasteners from corrosion. During tightening, however, this layer can break down and cause cold welding and clogging of the sliding interfaces. When galling occurs, the friction increases quickly at the expense of the preload achieved in the joint. Although lubrication can reduce both high frictional variation and galling, many assemblers forget to apply lubricant to the fastener before assembly. As a result, PV racking joints enter service with much lower preload than originally intended
SOLUTIONS: PRELOAD SCATTER
There are several ways to reduce preload scatter in threaded and lockbolt fasteners.
Threaded Fasteners
There are three obvious steps to reduce preload scatter in torque-tightened, threaded fasteners: one, improve the accuracy of the torque applied to the fastener during assembly by using more accurate torque tools, and two, improve the skill of the assemblers by training them on the proper use of the tools and assembly techniques. An often, overlooked third step is to control the friction coefficients of the fasteners using a lubricant, especially if the fasteners are stainless steel. Application of the lubricant can occur onsite by the assembler or applied in advance using a pre-applied dry film lubricant. After taking these three steps, the expected preload scatter with torque-tightened threaded fasteners will likely be no better than ±25% (see Diagram 5), assuming the target-tightening torque was determined from torque-tension testing and the assemblers follow the work instructions. [5] Verification that the fasteners were tightened correctly can be accomplished through residual torque audits. Although time consuming, these audits have been shown to be effective if conducted by a trained inspector.
Lockbolts
The simplest method of reducing the preload scatter is to eliminate the use of torque-tightened threaded fasteners altogether using lockbolts. Lockbolts are tensioned directly using accurate power tools that set the preload through the swaging process as shown in Image 6. The tooling and lockbolt design eliminate the effects of assembler skill and variations in the friction coefficients altogether and results in a relatively low preload scatter of approximately ±5% (see Diagram 5). [4,9] Lockbolts typically have shallower threads and larger cross-sectional area in the threaded region which allows them to be tightened to slightly higher preload too. As shown in Diagram 5, the mean preload for a 3/8” lock bolt (SAE J429 Grade 8 equivalent material) is 7,400lbf vs 6,975lbf for a 3/8-16 threaded bolt. Lockbolt assembly is relatively quick and easy and this reduces the assembler training time. Witness marks on the crimped collar provide a visual indication that the minimum preload was achieved during tightening, making auditing of lockbolts quick and easy.
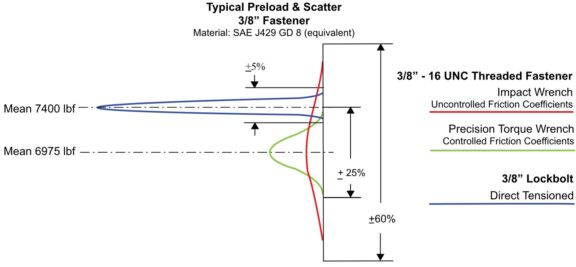
Re-tensioning of lockbolts is not possible so it is critical that relaxation effects in the joint be accounted for during the initial design process. Notably, dismantling of lockbolts requires a special cutting tool, which is commonly part of the installation tool.
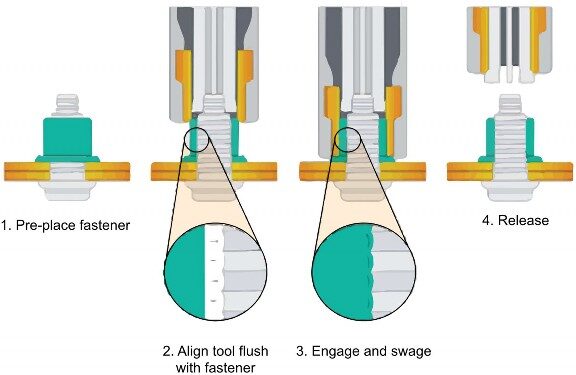
ISSUE: LOSS OF RESIDUAL PRELOAD IN SERVICE
Residual preload is what remains as clamp load in the bolt after the solar racking or tracking structure has been placed in service and exposed to external loading. Surprisingly, the residual preload can drop dramatically because of relaxation and self-loosening and this has been shown to be a source of many structural failures in the field. [1]
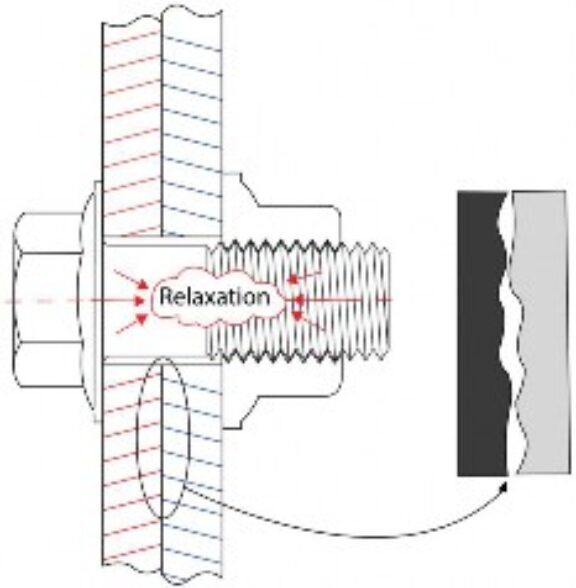
Loss of Residual Preload through Joint Relaxation
This loosening process occurs without rotation in the fastener, yet there is still preload loss caused by the localized plastic deformations within the joint load bearing surfaces (embedment). The surfaces of a joint interface and fastener threads appear to be smooth. Yet under a microscope, it becomes apparent that the surfaces consist of ridges or asperities and valleys as shown in Image 7. When two mating surfaces come together to create the joint, the microscopic ridges on both surfaces make contact and plastically deform.[3] Other sources of relaxation in PV racking system joints are the electrical bonding devices and serrated surfaces often placed in the joint to create grounding connections. Aluminum racking components are generally anodized to protect against corrosion and this anodized surface is a natural insulator, while the core aluminum remains electrically conductive. To ensure a continuous grounding connection, a bonding component is placed in the mounting system interface to pierce the outer anodized surface of the joint components after tightening. This connects the electrically conductive core aluminum in the mating components. Similar to embedment, the piercing of the anodized surfaces can lead to plastic deformation in the joint.
The initial tightening of a fastener results in a surprisingly small amount of elastic stretching within the fastener. In many fasteners the stretch is typically less than 0.001 inches, so the residual preload in the joint is highly sensitive to the plastic deformation. While relaxation mainly occurs during the tightening process, it also continues after the tightening is complete and especially during the initial loading cycles. Assuming the fasteners and the joint are tightened below their yield point, the relaxation in the joint will subside. However, since most PV joints are not retightened after initial assembly, in-service relaxation can result in a significant loss of preload. In extreme cases, as much as 40% of the preload load can be lost because of in-service relaxation of PV racking system joints.
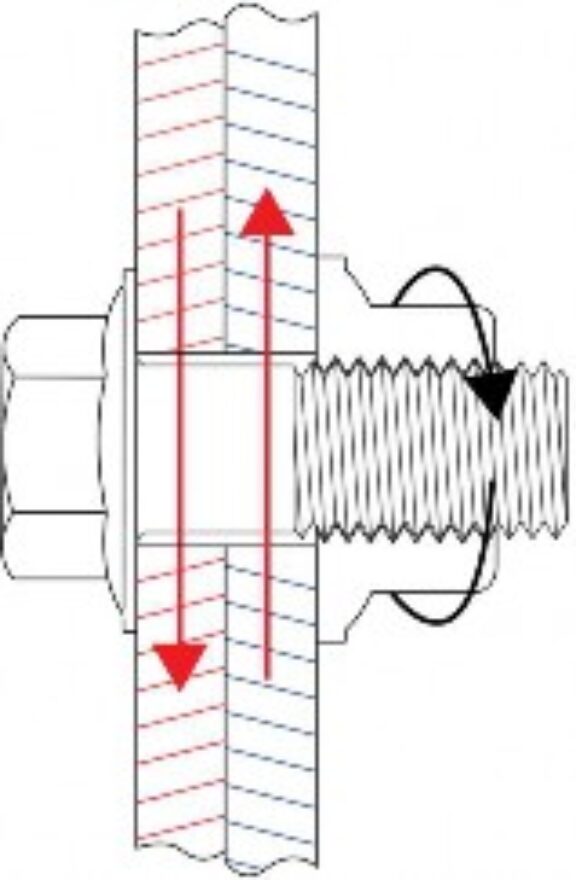
Loss of Residual Preload through Self-Loosening
Self-loosening takes place when the threaded fastener loosens by rotation as a result of repeated slippage in the joint, threads and fastener-bearing surfaces as shown in Image 8. [11] This slip will occur if the external shear force applied to the joint exceeds the friction grip generated by the fastener preload and friction coefficients in the joint. In PV racking joints, this can occur when the joint is repeatedly loaded in high wind events, but also at much lower loads, especially if the residual preload is lower than expected. Low residual preload is frequently caused by a wide scatter in the preload or because of the other relaxation effects discussed previously. [10] Self-loosening can be a significant problem in solar racking and tracking structures. In extreme cases, the fasteners have been shown to even fallout. [1]
SOLUTIONS: LOSS OF RESIDUAL PRELOAD IN SERVICE
There are numerous methods and commercial solutions to either reduce or prevent the loss of residual preload in service.
Joint Relaxation
The simplest approach to avoid joint relaxation is to retighten the fasteners in the system multiple times during the initial commissioning and over the course of the service life. Of course, repeatedly retightening the fasteners may not be realistic or even possible in some racking system installations because of the inaccessibility of the fasteners. Retightening lockbolts is not even possible. If retightening is not possible, then embedment and the associated preload relaxation must be reduced as much as possible through smart design choices.
One way to achieve this is by decreasing the number of interfaces within the joint. The fewer the joint interfaces, the less embedment and relaxation. Compared to conventional threaded fasteners that may require washers, lockbolts do not typically require washers therefore reducing the amount of relaxation experienced after installation. [2] Another option is to lower the stiffness of the fasteners so that they become less sensitive to embedment and plastic deformation. This can be accomplished by increasing the grip length of the bolt and joint. Regardless of the option chosen, the safety factors used for fasteners in PV racking systems should be high to account for the uncertainty surrounding relaxation in the joint.
Self-Loosening of Fasteners
Threaded Fasteners. Self-loosening will not occur in threaded fasteners if the residual preload/clamp load is high enough to resist the applied loading, thus preventing joint movement. Unfortunately, the level of anticipated applied loading during service is uncertain during extreme wind load events. As a result, many designers take additional steps to prevent self-loosening by locking the internal and external thread together for an added level of security. There are a wide range of commercially available devices to lock the internal and external threads together.. Some of these devices are more effective than others (see Image 9).
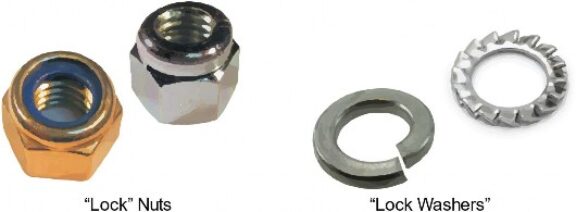
Fastener-locking device performance is typically evaluated using a transverse vibration test, otherwise known as a Junker test. [12] In this test, a simulated fastened joint is subjected to repeated transverse slip through a motor-driven cam (applicable standard: DIN 65151). Results show that standard nuts will loosen relatively quickly when exposed to transverse slip using this test. [10] Similarly, prevailing torque ‘lock’ nuts and ‘lock’ washers loosen relatively quickly. [11]
This test shows that the best-performing locking devices for the threaded fasteners used in PV racking systems are wedge washers and pre-applied, high-strength thread adhesives as shown in Graph 10.
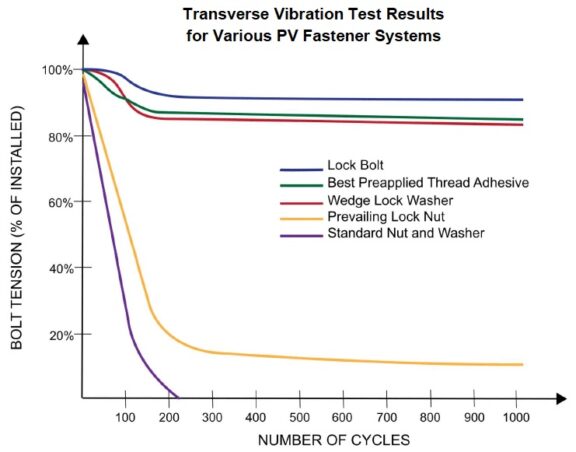
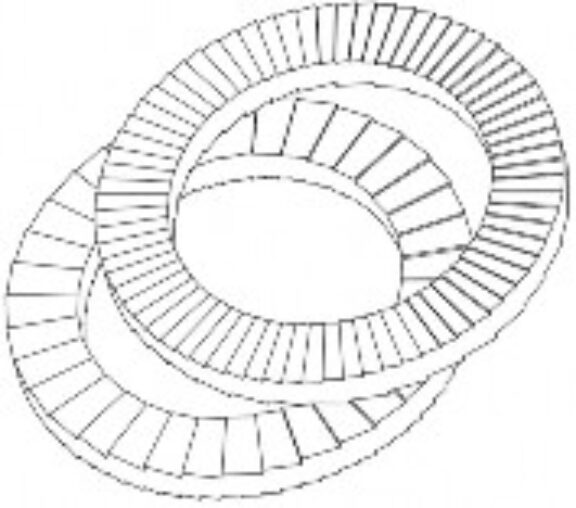
Wedge washers consist of a pair of hardened washers with cams on one side and serrations on the other, as shown in Image 11. The serrations on the outside of the washer bite into the joint surfaces, and the cam surfaces within the washer pair lock the fastener by a wedging action. Wedge washers must be assembled in pairs in a specific orientation. To facilitate assembly, the washers are typically received pre-oriented and glued together with a weak adhesive. Fasteners that are secured with wedge washers resist self-loosening through this action and yet can be retightened or disassembled if necessary. Unfortunately, wedge washers must be used at both the nut and bolt-bearing surfaces, which creates a lot of loose parts and slows down the assembly process. Another disadvantage of the design is the increased relaxation in the joint when the serrated surface on the washer plastically deforms the racking joint and bolt/nut bearing surfaces.
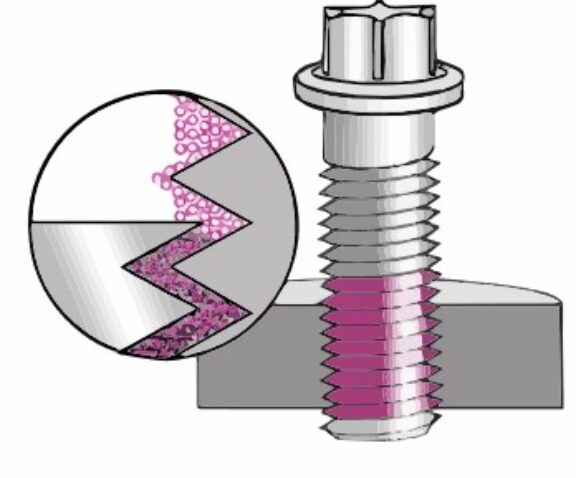
There are many pre-applied, high-strength thread lockers and adhesives to choose from. Unlike common “applied at assembly” thread lockers, a pre-applied adhesive is added to the threads at the factory, so the threaded fasteners can be assembled using standard processes. The highest strength adhesives typically contain microencapsulated beads of epoxy resin and expanding compound suspended in a hardener as shown in Image 12. When the fastener is installed, the microencapsulated beads break, releasing the adhesive and initiating the curing process. Modern formulations of the adhesive allow the fastener to be assembled at relatively low temperatures, and the adhesive typically cures within 24 hours after assembly. To ensure the highest strength bond, steps must be taken to make sure the mating nuts are clean and free of lubricant. Unfortunately, the highest-strength thread adhesives are permanent, and the locked fasteners cannot be retightened or disassembled without being damaged. This also means that it is not possible to conduct residual torque audits with this self-loosening solution.
Lockbolts. Given the nature of their design, lockbolts are immune from self-loosening since the internal and external threads are crimped (locked) together during the assembly process. Similar to high-strength adhesives used with threaded fasteners, lockbolts are generally permanent. Although they cannot be retightened, they can be disassembled quickly with special tooling which splits the collar.
CAUTION
While the use of threaded fastener locking devices, adhesive, or lock bolts may prevent self-loosening from occurring in service, they will not prevent the joint from slipping if the preload (clamp load) in the joint is insufficient to carry the shear loads. As a result, both threaded fasteners and lockbolts may experience repeated bending loads if the joint slips and so may be prone to fatigue failure. Caution should be used in threaded fastener locking devices or lockbolts in applications where the joint is overloaded and slipping or opening. Regardless of whether threaded fasteners or lock bolts are used, the most effective method to prevent self-loosening is to ensure the residual preload/clamp load is high enough to resist the applied loading and prevent the joint from slipping.
CONCLUSION
Fasteners in PV racking systems are often overlooked even though they play a significant role in the structural integrity and reliability of the system. This is evident by the requirements defined in UL 2703 for fastened joints. Traditional threaded fasteners are commonplace and relatively low cost, yet the threaded connection can be a significant source of issues in PV racking system installations unless deliberate precautions are taken during design, procurement, and assembly.
Lockbolts have several advantages over traditional threaded fasteners for connecting permanent PV racking system joints, as shown in Table 13. Given the large number of fasteners in a typical PV racking system, lockbolts are generally considered a superior alternative to threaded fasteners where the expense of special installation tools and equipment can be justified. Lockbolts are tensioned directly using accurate power tools, resulting in relatively high preloads and low scatter (approximately ±5%). Auditing the assembled lockbolt joint is relatively easy because of the witness marks on the crimped collar, which provide a visual indication that the minimum preload was achieved during tightening. Compared to conventional threaded fasteners that may require washers, lockbolts do not typically require additional washers. This potentially reduces the amount of relaxation experienced after tightening. Lastly, by the nature of their permanent design, lockbolts are immune from the self-loosening process without additional locking devices or thread adhesives.
Table 13 – Comparison of Torque-Tightened Threaded Fasteners and Lockbolts
TORQUE-TIGHTENED THREADED FASTENER | LOCKBOLT | |
---|---|---|
Initial Preload Scatter | Preload scatter of a torque-tightened threaded fastener and range from ±20% on the low end to as much as ±60% on the high end. | The preload scatter of lockbolts is generally considered to be approximately ±5% |
Assembler Training Requirements | Assembler skill plays an important role in controlling preload scatter so ongoing training is generally required. | Generally minimal. |
Speed of Assembly | Highly dependent on the skill of the assembler and their tools. | Lockbolts can often be assembled in less than 5 seconds. |
Risk of Galling of Stainless Steel Fasteners | High | Minimal because of the direct tension method. |
Resistance to Self-Loosening | Not resistant to self-loosening unless a wedge lock washers or pre-applied, high strength thread adhesives are used. | Given the nature of their design, lockbolts are immune from the self-loosening since the internal and external threads are crimped (locked) together during the assembly process. |
Residual Torque Auditing | Residual torque audits have been shown to be effective if conducted by a trained inspector. It is not possible to conduct residual torque audits if high-strength thread lockers and adhesives used. | Witness marks on the crimped collar provide a visual indication that the minimum preload was achieved during tightening, making auditing of lockbolts quick and easy. |
Ability to be Retightened | Yes, unless if high-strength thread lockers and adhesives used. | No |
Tightening Tool Cost | Relatively low. | The expense of the special installation tools and equipment required for assembly could be uneconomic for small quantities but that is generally not an issue with PV racking systems given the number of fasteners. |
The information contained in this paper is intended for training and reference purposes only. Do not rely solely on this information as guidance for any application. Always independently verify any technical information through an authoritative source before using it in a specific application. The reader is solely and exclusively responsible for any consequence, intended, or unintended, deriving from the use or misuse of this material, and the author shall have no liability therefor.
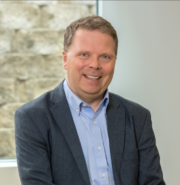
Jon Ness
PE, PMP, NPDPJon is a Managing Governor and Principal Engineer at Matrix Engineering and has over 34 years of experience in business and engineering team leadership. His career has been focused on the development of off-highway equipment and powertrains. He has unique technical expertise in designing and validating dynamically loaded bolted joints. In his consulting role, Jon has led numerous joint failure investigations, including re-design efforts to mitigate risks to the system owners. He actively participates in ongoing research projects and has taught many classes related to Failure Modes and Effects Analysis and Bolted Joint Design and Validation. He received a Bachelor of Science in mechanical engineering from South Dakota State University. A licensed engineer in Minnesota, Jon is an active member of the UL2703 Standards Technical Panel, a contributor to the ASCE Manual of Practice for Solar PV Structures, and a Certified Fastener Specialist through the Fastener Training Institute.
REFERENCES
- Robinson, G. “Solar Photovoltaic Systems in Hurricanes and Other Severe Weather.” US Department of Energy, Office of Energy Efficiency and Renewable Energy, 2018.
- Ebert, Dorre and Gliencke. “Behavior of lockbolts in slip-resistant connections for steel structures.” Steel Construction Design and Research, Ernst & Sohn, Berlin, 2017
- VDI 2230 (Part 1): “Systematic calculation of highly stressed bolted joints.” Beuth Verlag, Berlin, Nov 2015.
- DVS Technical Committee, Mechanical Engineering Working Group). “Lockbolt systems – calculation of connections according to Eurocode 3 and VDI 2230 Part 1.” Bezant: DVS Media, Dusseldorf, 2017.
- Brown, KH, et al. “Guideline for Bolted Joint Design and Analysis: Version 1.0.” Sandia National Laboratories, Albuquerque, NM, and Livermore, CA, 2008.
- Eccles, W. “Design Guidelines for Torque Controlled Tightening of Bolted Joints – 930578.” Society of Automotive Engineers, Warrendale, PA, 1993.
- Kulak, GL, Fisher WJ, and Struik, JHA. “Guide to Design Criteria for Bolted and Riveted Joints.” Research Council on Structural Connections, Chicago, 2001.
- Rogers, M and Phillips, R. “Tracking Your Solar Investment: Best Practices for Solar Tracker O&M,” NEXTracker, Fremont, Calif., 2017.
- “Torque vs Clamp. Arconic Fastening System and Rings.” 2011
- Eccles, B. “Self-loosening of threaded fasteners,” Fastener Fix Technology. 2011
- “Threadlocker User’s Guide – What you need to know to ensure a reliable threaded assembly,” Henkel
- Junker, G. “New Criteria for Self-Loosening of Fastener Under Vibration”. Transactions of the Society of Automotive Engineers, Warrendale, PA 1993.
Looking for a collaborative partner?
Whether you’re innovating from the ground up or enhancing an existing product, Matrix Engineering is here to guide you. Our team excels in providing dynamic solutions for new developments, improvements, and complex challenges across various industries.
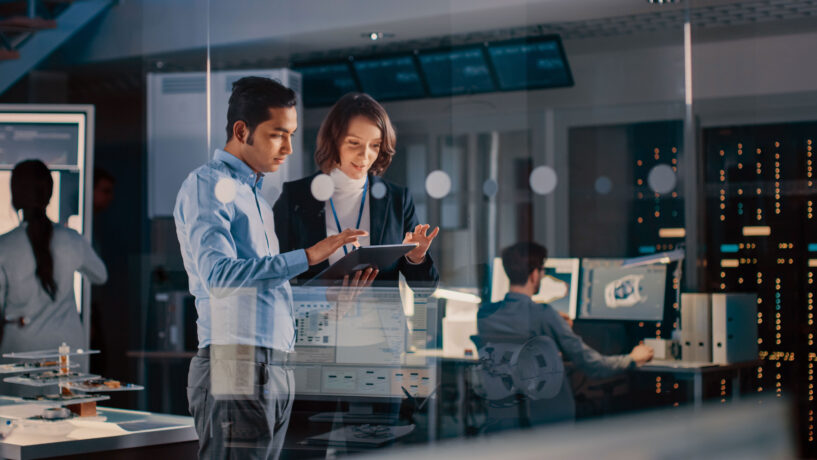